フライス加工とは?種類や加工方法をわかりやすく解説!
フライス加工は、製造業において欠かせない金属加工技術のひとつです。回転する切削工具を用いて、金属や樹脂などの材料を削り、精密な部品を作り上げる加工方法です。自動車部品から航空機部品に至るまで、私たちの身の回りにある多くの製品が、フライス加工によって製造されています。
この記事では、フライス加工の基本概念から具体的な加工方法、使用される機械や工具について詳しく解説していきます。
フライスとは
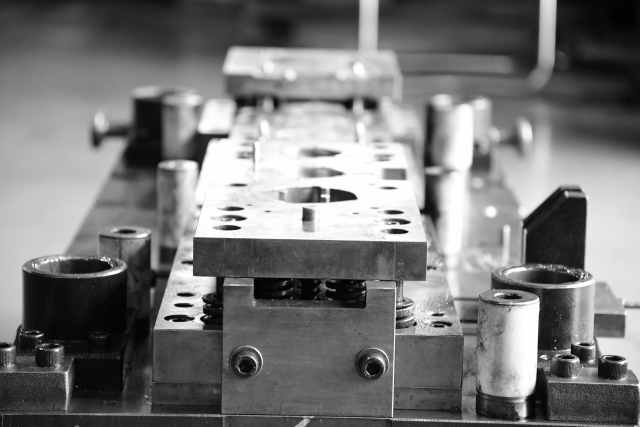
フライスとは、円筒状の形をした複数の刃を持つ切削工具のことを指します。工具を高速回転させながら、固定された材料に当てることで不要な部分を削り取る加工方法がフライス加工です。
旋盤との違い
フライス加工と旋盤加工の大きな違いは、何を回転させるかにあります。フライス加工では切削工具を回転させ、材料は固定したまま加工を行います。
一方、旋盤加工では材料を回転させて、固定した工具で削っていく方法です。フライス加工は角ばった形状や平面の加工を得意とし、旋盤加工は円筒形状の加工に適しています。
フライス盤の種類
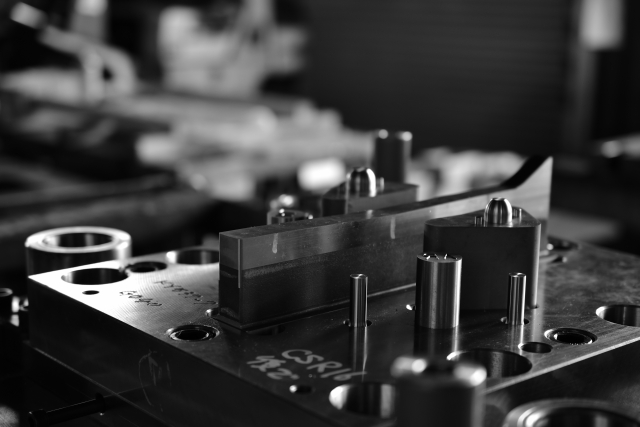
フライス加工を行うための機械であるフライス盤には、構造や操作方法によって複数の種類があります。
ここでは、立フライス盤から最新のマシニングセンタまで、各フライス盤の特徴と用途について解説します。
立フライス盤
立フライス盤は、切削工具を取り付ける主軸が垂直方向に配置されたフライス盤です。工具が上から下に向かって材料を削るため、平面加工や穴加工などの作業に適しているのが特徴です。テーブル上に材料を固定し、主軸を上下に動かしたりテーブルを前後左右に移動させたりして加工を行います。操作がしやすく視認性も良いため、試作品の製作や小ロット生産などで広く使用されています。
横フライス盤
横フライス盤は、主軸が水平方向に取り付けられているフライス盤です。工具が横向きに回転するため、厚みのある材料の側面加工や長い溝の加工に優れた性能を発揮します。切りくずの排出性が良く、深い穴や溝の加工でも効率的に作業を進められるのが特徴です。
また、板状の材料の側面を削る場合には、横フライス盤でなければ加工できない形状もあります。立フライス盤に比べて剛性が高いため、重い材料や力のかかる加工にも適しています。
万能フライス盤
万能フライス盤は、立フライス盤と横フライス盤の両方の機能を持った多機能なフライス盤です。主軸が回転や傾斜ができるため、斜めの面や複雑な角度の加工も可能です。
テーブルが水平方向にも回転できるため、一台でさまざまな角度からの加工が可能です。歯車のような複雑な形状や、複数の角度が必要な部品の加工に適しています。多様な加工に対応できる反面、操作には高い技術と経験が求められ、習得には時間を要する点が特徴です。
汎用フライス盤
汎用フライス盤は、すべての操作を作業者が手動で行うタイプのフライス盤です。
工具の取り付けから材料の固定、切削条件の設定まで、すべて人の手で調整します。プログラム作成の必要がないため、すぐに加工を始められます。
作業者の技術と経験によって仕上がりが大きく左右されるため、熟練した技術者が扱えば高精度な加工も可能です。試作品や特注品など、少量生産に向いている機械ですが、大量生産には効率的ではありません。
NCフライス盤
NCフライス盤は、数値制御(Numerical Control)によって自動加工を行うフライス盤です。
あらかじめプログラムされた数値データに基づいて、工具やテーブルの動きを正確に制御します。作業者の技量に左右されることなく、安定した品質の製品を効率的に製造可能です。
複雑な形状も高精度で加工でき、同じ製品を大量に作る場合に威力を発揮します。導入コストは汎用フライス盤より高くなりますが、プログラミング技術を習得すればさまざまな加工に対応できる優れた機械です。
マシニングセンタ
マシニングセンタは、NCフライス盤に自動工具交換装置(ATC)を搭載した高度な加工機械です。
複数の工具を自動で交換しながら、一つの材料に対してさまざまな加工を連続して行えます。穴加工から平面加工、溝加工まで、工具を手動で交換することなく完成品まで仕上げることが可能です。加工精度が高く効率的な生産ができるため、現代の製造業では中心的な役割を果たしています。操作には専門知識が必要ですが、習得すれば非常に生産性の高い加工を実現できます。
フライス盤で使用される工具
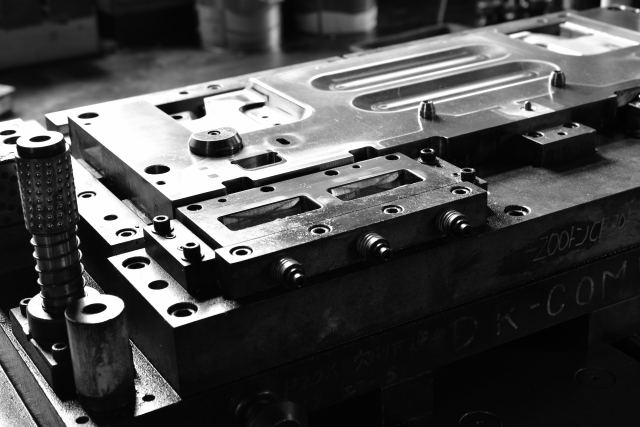
フライス加工では、加工したい形状や材料に応じて様々な種類の切削工具を使い分けます。
ここでは、代表的なフライス工具の特徴と用途について解説します。
正面フライス
正面フライスは、円の外周部分に多数の切れ刃を持つボアタイプの工具です。フェースミルとも呼ばれ、主に材料の表面を平らに削る平面加工に使用されます。一度に広い範囲を効率的に削れるため、大きな平面の加工に適しています。
外径が大きくなるほど一度に削れる面積も増えますが、その分機械に必要な出力も大きくなります。立フライス盤で最も多く使用される工具で、高精度な平面を短時間で仕上げることができる優れた工具です。
エンドミル
エンドミルは、ドリルのような細長い棒状の形をしたシャンクタイプの工具です。先端から側面にかけて切れ刃があり、平面加工から側面加工、段加工、溝加工までさまざまな用途に使える万能工具です。
スクエアエンドミルやボールエンドミルなど、先端形状の違いによっていくつかの種類があります。細かい部分の加工や複雑な形状の製作に優れており、一本の工具で多様な加工ができるため工具交換の手間を省けます。
平フライス
平フライスは、円筒形状の外周面に切れ刃を持つボアタイプの工具です。プレーンカッターとも呼ばれ、主に横フライス盤で平面加工を行う際に使用されます。カンナがけのように材料の表面を平らに整える作業に適しており、広い面積を効率的に削ることが可能です。
正面フライスと比較すると切削効率は良いものの、加工精度では劣るため、主に粗削り加工に用いられます。厚みのある材料や、大きな平面を素早く削りたい場合に威力を発揮する工具です。
フライス加工でできること
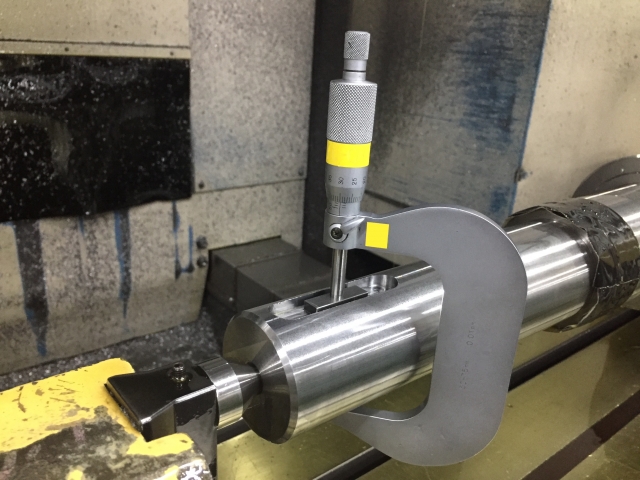
フライス加工は、切削工具を使い分けることで非常に多様な形状を作り出せる加工方法です。
ここでは、フライス加工で行える代表的な加工方法について解説します。
平面切削
平面切削は、材料の表面を平らに削る最も基本的な加工方法です。
正面フライスやエンドミルを使用し、テーブルを前後左右に動かしながら工具を材料に当てて削ります。一般的には、広い面積を効率的に加工できる正面フライスが用いられますが、狭い範囲や細かい部分の加工にはエンドミルが適しています。
表面の凹凸を取り除いて滑らかな仕上がりにしたり、寸法を正確に整えたりする際に行われる、機械部品加工の基本となる工程です。
側面切削
側面切削は、材料の側面部分を削って垂直な面を作る加工方法です。
工具を上下に動かしながらテーブルを移動させることで、材料の端面や側面を整えます。エンドミルを使用するのが一般的ですが、広く浅い段差を作る場合には正面フライスを用いることもあります。
R面(曲面)も含めて美しく仕上げることができ、部品の外観や寸法精度を向上させる効果があります。箱型の部品や角材の加工において、直角な面を正確に作り出すために欠かせない加工技術です。
段加工
段加工は、材料に段差を付ける加工方法で、平面加工と側面加工を組み合わせた技術です。
まず平面を削った後、さらに一段深く掘り下げるように工具で削ることで段差を作ります。広い面積や低い段差には正面フライスを使用し、狭い面積や高い段差にはエンドミルを使用します。
階段のような形状を作ったり、部品の一部を薄くしたりする際に用いられます。複雑な立体形状の部品を作る際の基本技術として、多くの製造現場で活用されている重要な加工方法です。
溝加工
溝加工は、材料の表面に溝を掘る加工方法です。
エンドミルを使用して指定の深さまで削った後、テーブルを移動させて溝の形状を作ります。直線的な溝だけでなく、T字型の溝や台形のアリ溝なども専用の工具を使って加工できます。
ボルトを固定するためのT溝や、部品同士を組み合わせるための嵌合溝など、機械部品には欠かせない形状です。溝フライスという専用工具を使えば、エンドミルよりも効率的で高精度な溝加工が可能になります。
穴加工
穴加工は、材料に円形の穴を開ける加工方法です。
ドリルを使用して穴を開けるのが基本的な方法ですが、エンドミルを螺旋状に動かすことで、大きな穴を開けることも可能です。まずセンター穴ドリルで位置決めを行い、その後、本ドリルで指定の深さまで穴を開けます。
ボルトを通すための貫通穴や、部品を組み立てる際の位置決め穴など、用途は多岐にわたります。面からの位置精度が求められる場合には、エンドミルを使用することで工具交換の手間を省き、面と穴を連続して加工することが可能です。
フライス加工を行う際の注意点
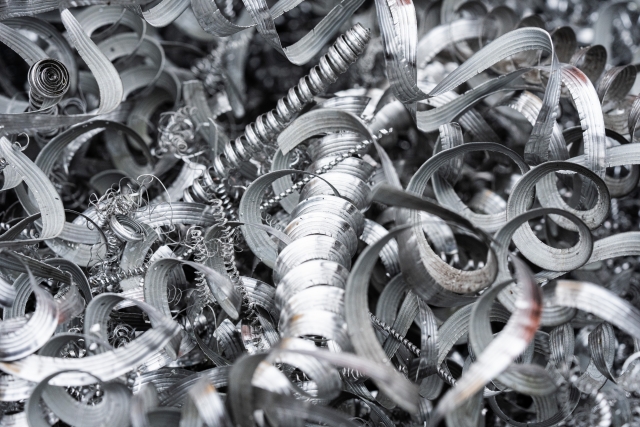
フライス加工を安全かつ正確に行うためには、いくつかの重要な注意点があります。
ここでは、フライス加工を行う際に特に注意すべきポイントについて解説します。
加工内容によっては難易度が高いこともある
フライス加工は多様な形状に対応できる優れた技術ですが、苦手とする加工もあります。特に「ピンカド」と呼ばれる、凹形状の角が完全に直角になる部分の加工は困難です。回転する工具を使用するため、どうしても工具の円弧部分が残り、完全な直角を作れません。
その場合は、放電加工やワイヤーカット加工など、他の加工方法を組み合わせる必要があります。設計段階で角に丸みを付けたり、逃げ部分を設けたりして、フライス加工で対応できる形状にすることが重要です。
切削工具の選定と管理をしっかり行う
適切な工具選択は、加工品質と効率を左右する重要な要素です。加工する材料の種類や硬さ、求められる精度や加工形状に応じて、良い工具を選定する必要があります。また、摩耗や欠けのある工具を使用すると、加工精度が著しく低下するだけでなく、工具の破損や機械への損傷を招く危険性があります。
定期的な工具の点検と交換を行い、常に良好な状態を保つことが大切です。工具の寿命を把握し、適切なタイミングで新しい工具に交換することで、安定した品質の製品を製造できます。
ワークの固定と安全対策を行う
加工中に材料が動いてしまうと、加工精度の低下や重大な事故につながる可能性があります。バイスやクランプなどの固定具を使用して、材料をしっかりと固定することが必須です。固定が緩すぎると材料が飛んでしまい、逆に締めすぎると材料が浮いて精度が悪化する恐れがあります。
材料の大きさや形状、重量を考慮して適切な固定方法を選択し、適度な力で固定することが重要です。また、切りくずの飛散防止や保護具の着用など、作業者の安全を確保するための対策も欠かせません。
まとめ
フライス加工は、回転する切削工具を用いて金属や樹脂を精密に削る重要な加工技術です。さまざまな機械と工具を使い分けることで多様な形状を実現でき、現代の製造業を支える基盤技術として活用されています。適切な工具選択と材料固定により、安全で高品質な加工を実現できます。